Magnetic Particle Testing (MT): Fast, Reliable Surface Crack Detection
Magnetic Particle Testing (MT) Magnetic Particle Testing (MT) represents the best known and the most successful technique of non-destructive testing (NDT). It also directly causes the detection of the surface and near-surface of magnetic substances. Safety, as well as structural credentials of all those industries, require all of those goals. The environments in some of the places where the MT is extensively used include the oil and gas, marine, building, and manufacturing industries, where the impetus of operation is very important. To make sure that the precision of defects is precise and that we can get a constructive lesson regarding the integrity of your material, discover our detailed Magnetic Particle Testing (MT) services that would suit your kind of industry.
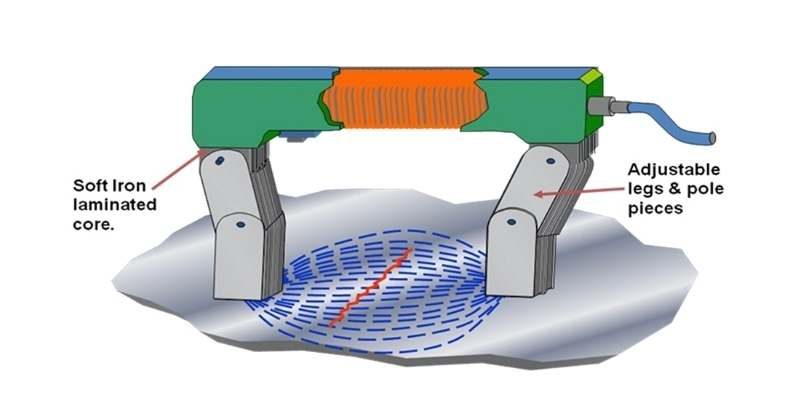
What is magnetic particle testing (MT)?
The basis of Magnetic Particle Testing(MT) is the principle of magnetism, and the test is used in the detection of discontinuities on the surface and essentially near the surface. And the procedure starts by magnetizing the material in such a way that it would produce a magnetic field. In the case where there is discontinuity, i.e, a crack, inclusion, etc., the magnetic field will be disturbed and it will cause leakage of the magnetic flux.
These are in fine particulate form, and the particles are made of ferromagnetic material, and this can be deposited in sealed or liquid solution form ( the dry and wet MT procedures ) and sprayed on the surface. These particles also accumulate at the site of the leak and leave an account of the damage behind. That is the reason why MT may be of immense help in bringing to light the cracks and the flaws on the surface.
Note: MT could work only with the magnetizable materials (ferromagnetic), e.g., with iron, nickel, cobalt, or alloys. It is a key method in the wider area of non-destructive testing.
Applications of MT in Industry
MPT is widely and highly used in many industrial sectors. It is quite helpful in displaying surface-level and near-surface conditions and, therefore, ensuring certain integrity and good quality control of the assets.
- Weld inspection of steel structures and pipelines: This is vital in the inspection of surface-breaking flaws in welded joints like cracks, incomplete fusion, and no penetration.
- Surface defect detection in castings and forgings: This can be used to detect major manufacturing defects such as shrinkage cracks, seams, laps, and hot tears to be machined or assembled.
- Fatigue cracks in the machinery parts: There is a dire need to identify the presence of fatigue cracks in highly stressed areas like shafts, gears, engine parts, and nozzles of pressure vessels during routine maintenance, as well as during the overhaul.
- In-service inspection of offshore and marine equipment: An example that has been widely deployed to inspect ship hulls, drilling rigs, platforms, and other important marine installations for integrity evaluation.
- Maintenance checks during fabrication and shutdowns: An invaluable system of identifying defects in the factory during different phases of manufacture, as well as at routine maintenance, and ensuring the avoidance of expensive breakdowns.
Key Advantages of Magnetic Particle Testing
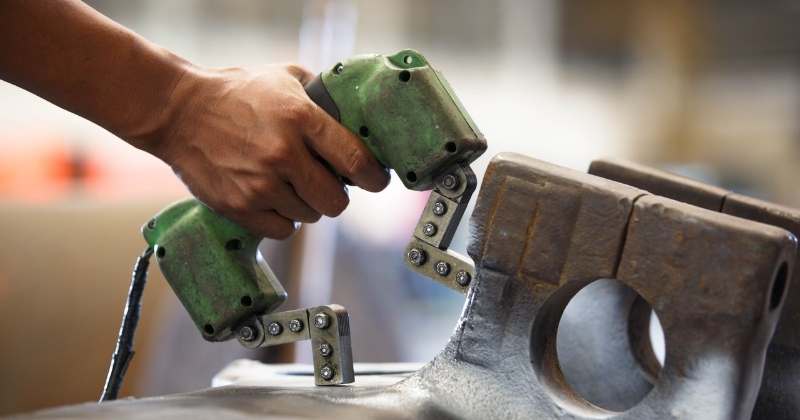
1. High Sensitivity to Surface Flaws
MT is very sensitive. It can see very minute and superficial cracks on the surface; even the ones not observable by the naked eye are detected. This great precision is quite essential to spot vital discontinuities early enough before they spread and result in serious structural problems.
2. Quick and Efficient
In comparison with numerous other NDT techniques, magnetic particle testing is comparatively quick and real-time. This benefit is used to verify in-service inspection plans and heavily planned projects of large spaces or multiple parts as they can be inspected easily.
3. Non-Destructive and Safe
As a non-destructive test method, MT tests components without causing any damage or alterations to their form. This is spent on the functionality and the durability of the object under inspection. This test also turns out to be a safe process when a test is conducted by professionally certified individuals who also follow strict security instructions.
4. Versatile for Various Applications
MT proves itself to be very versatile. It applies to all sizes and intricate shapes of the components, small fasteners, bolts, huge structural welds, and complicated castings. This renders it very flexible in various different industrial uses in a large mix of fields.
5. Visual Indications for Easy Interpretation
Among the most useful advantages of MT is the fact that the defects it identifies are in the form of apparent, visible concentrations of magnetic materials. This simplifies the interpretation of inspection results and, in many cases, means that very complex or specialized analysis equipment is unnecessary. Such direct visibility is very helpful in the rapid inspection of welds and overall flaw identification.